Low Speed Gearboxes are motorized drive systems that convert electrical energy into mechanical power for use in equipment control. Used primarily in industrial settings where consistent output of power is essential, these gearboxes also reduce noise generated by machinery while protecting against shocks and vibration. When designing applications involving Low Speed Gearboxes it is vital to understand their relationship to one another as they must work in concert to deliver optimal performance.
A gearbox must produce sufficient torque to drive any machinery it connects with, even when not fully loaded. Furthermore, it must be capable of accommodating sudden load surges and jams that may arise within machines as well as sudden acceleration torque spikes. Finally, its ratio between speed and torque must suit its application perfectly.
To optimize the efficiency of a gear drive, it is critical to carefully consider its shaft arrangements, bearing types and lubrication needs. A shaft arrangement refers to where high and low speed shafts sit relative to one another based on factors like available space in an application and the positioning of drives and driven equipment.
Dependent upon the shaft configuration, there are various gear drive configurations to consider when choosing gear drives. A right angle gear drive has high and low speed shafts arranged at 90 degree intervals - an arrangement often used on conveyors; furthermore this drive type is great when space is at a premium and equipment must be mounted close by.
Shaft orientation on a gearbox can have a dramatic effect on torque output, with parallel drives typically providing optimal results at lower speeds while right angle drives deliver higher efficiency at higher ones. Lubrication also plays an important role, while number of gears in a drive has its own affects.
An increased moment of inertia on a gearbox can make motor starting and acceleration more challenging, which poses problems in robotic applications that demand responsive speed control. Therefore, selecting one with low moments of inertia is key.
Precision capability should also be taken into account when choosing a gearbox for robotic applications. A gearbox with low losses and nonlinear friction behavior allows for precise position control applications, providing ideal control options.
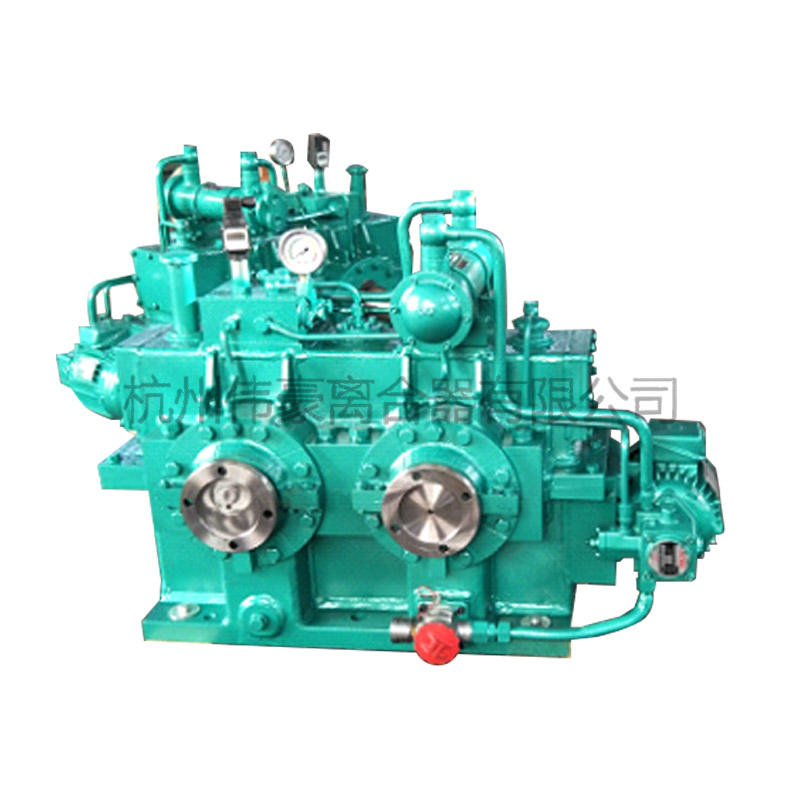
J302C/J302D low-speed experimental bench gearbox