Gearboxes are essential components of many industrial applications. From power generation, oil/gas exploration/production/refining operations and refining to pipeline/pumping applications, high-speed gearboxes require meticulous design and manufacturing standards to ensure maximum reliability in harsh environments ranging from the North Sea offshore platforms to frozen tundras in Canada - but Philadelphia Gear high-speed drives have an outstanding track record of long-term performance despite these obstacles.
An important function of any gearbox is producing torque. To achieve optimal operation, it is vital to match motor input power to driven load power requirements closely so the gearbox is able to provide sufficient torque during normal operational use. This is especially crucial during start-up when torque demand can be higher than typical level, jams, or load shocks when this torque requirement may exceed its nominal capacity of the gearbox.
Ideal gearbox sizing requires operating within factory specifications with loads that fall at or below its maximum load rating; this will maximize speed and efficiency while prolonging gears' and components' lives.
Gearbox design criteria includes considerations such as gear size, ratio, bearing diameters, using a central shaft for support, dampers to prevent vibration or oscillation and hardened and treated gears to provide high resistance against wear, corrosion and distortion. Spur, helical and bevel gearing options may be suitable depending on your application needs; generally larger gears tend to offer greater torque capacity due to greater radii and thus twisting forces.
Moment of inertia (MOI), which refers to a gearbox's resistance to acceleration, should also be carefully considered when choosing gearboxes for applications requiring responsive speed control such as robotic servosystems. A low MOI will prove indispensable.
Lubrication is another key component of gearbox operation and must be provided continuously to the tooth meshes and bearings of the gearbox. Both type and method must be chosen carefully in order to ensure proper functioning, as any build-up of heat during operation could damage gears and system components prematurely; furthermore, hardened and treated gears must also be hardened in order to reduce Hertzian stress which could cause cracking or warping of these critical system components.
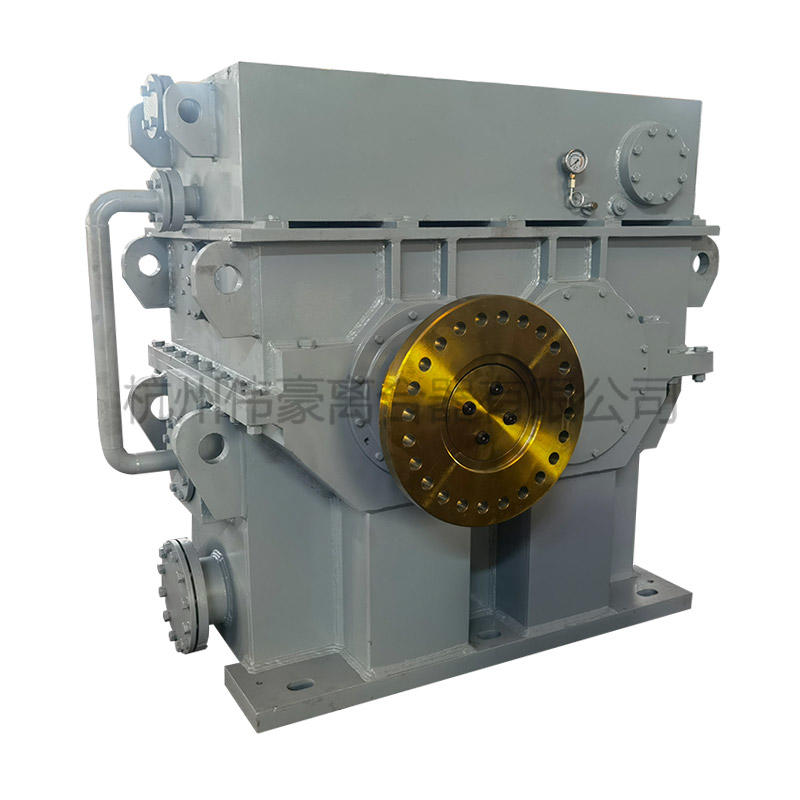
HGS500 high-speed gearbox